방짜 (Bangjja), homegrown
bronzecraft.
For multiple decades Korea’s Jong Duk Lee has been pursuing
perfection in the ancient craft of
bangjja, which is a unique form of metal
work.
Bangjja comes from the Napcheoung region, a northern part of Korea, where
it was originally used to make bell instruments and also tableware and crockery. Lee has dedicated much of his
life to applying the
bangjja technique to traditional instrument and object
making, earning an intangible heritage qualification in Korea. He also encourages others to pick up the
remarkable craft through education of younger artisans,
but today 80% of all the
bangjja instruments (such as
jing and
kkwaenggwari) made in Korea are by Lee.
Based in Tokyo, Ryutaro Yoshida has similarly pursued a career dedicated to craft
in Japan as the co-founder of
Time & Style - a
respected design and furniture brand. It produces pieces for famous architects such as Kengo Kuma and sells
its designs through various retailers across the world. For Yoshida, Time & Style is defined by its close
relationship to the craft
culture of Japan and he enjoys working alongside artisans across the nation to form products that honour the
past but are also appealing to a contemporary audience.
With this in mind,
Yoshida was interested in
speaking with Lee about bangjja, a craft he’s curious to learn more about.
It’s also a craft form that could die out – something that Yoshida’s work in Japan aims to prevent for its
craftspeople. Younger
generations have not been able to move bangjja forward and the Korean
government is not giving the craft enough support. But there is immense importance in bangjja - with its
incredible history and the meticulous making process behind it, it forms some of Korea’s most beautifully
made products, as Yoshida and Lee discuss.
- 1. Hand-forged plates in different forms
- 2. Traditional Korean spoon and chopstick set
- 3. Detail of 항아리 (hangari)—a small jar with Jong Duk
Lee's signature
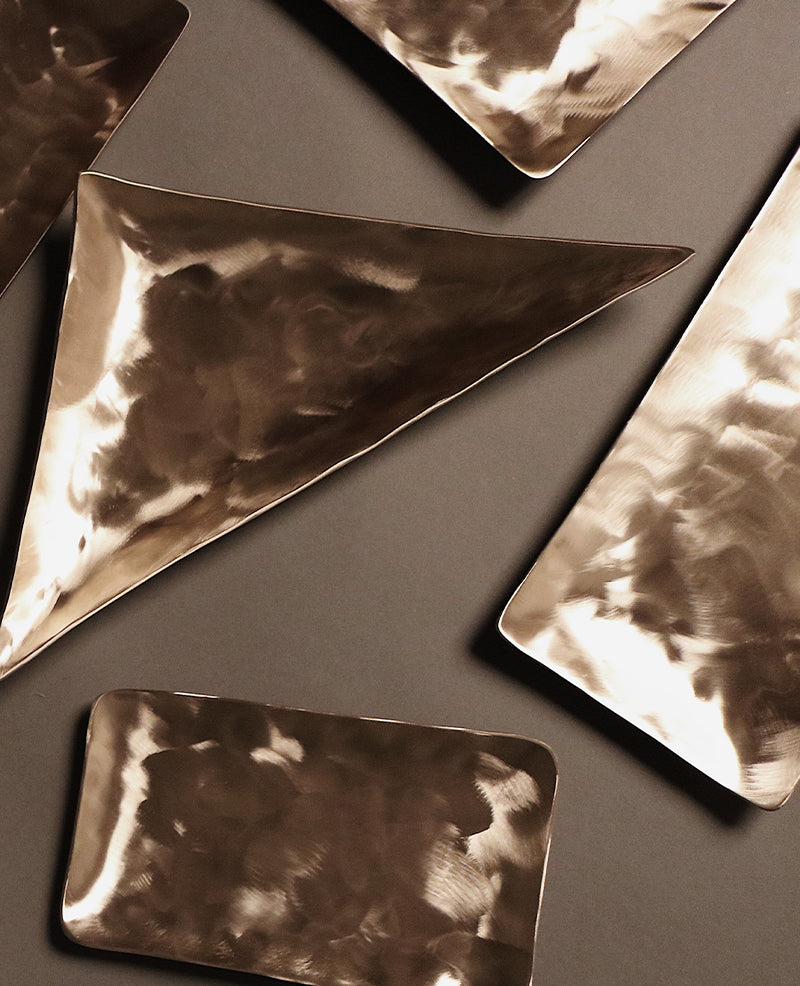
1.
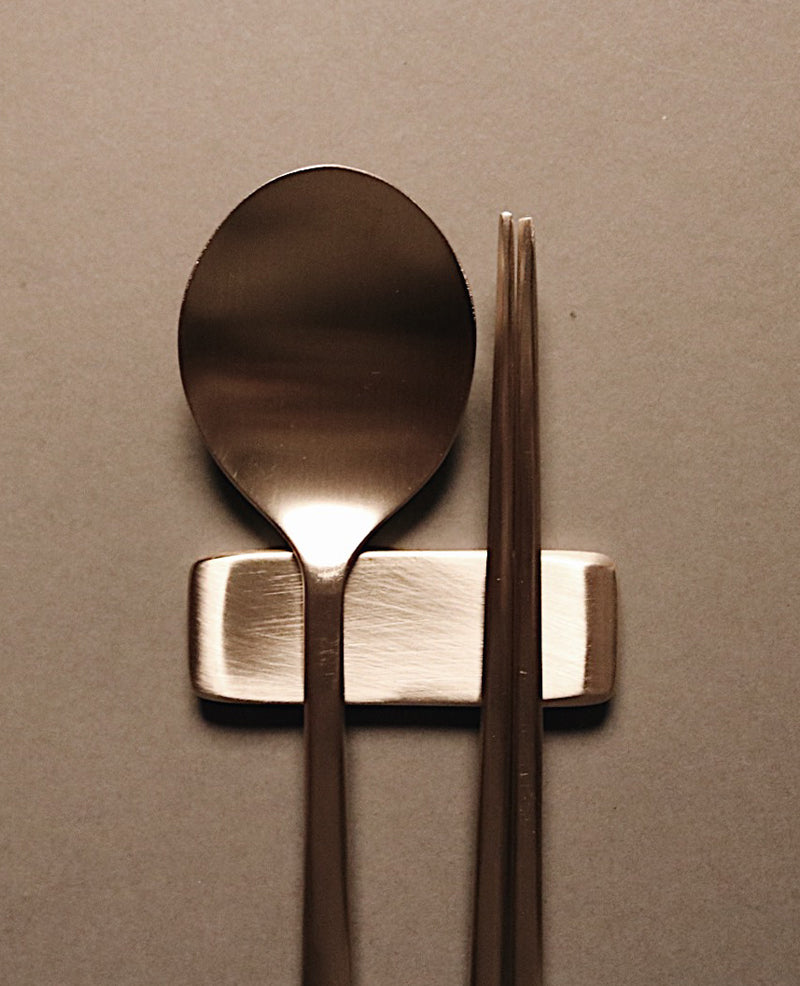
2.
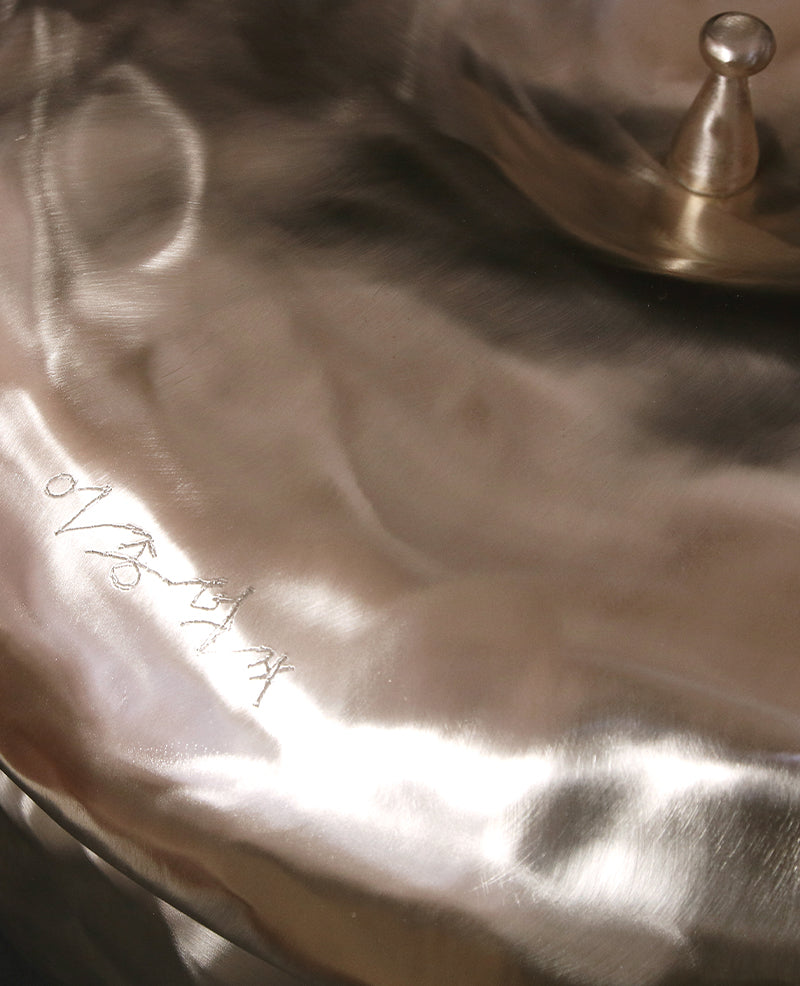
3.
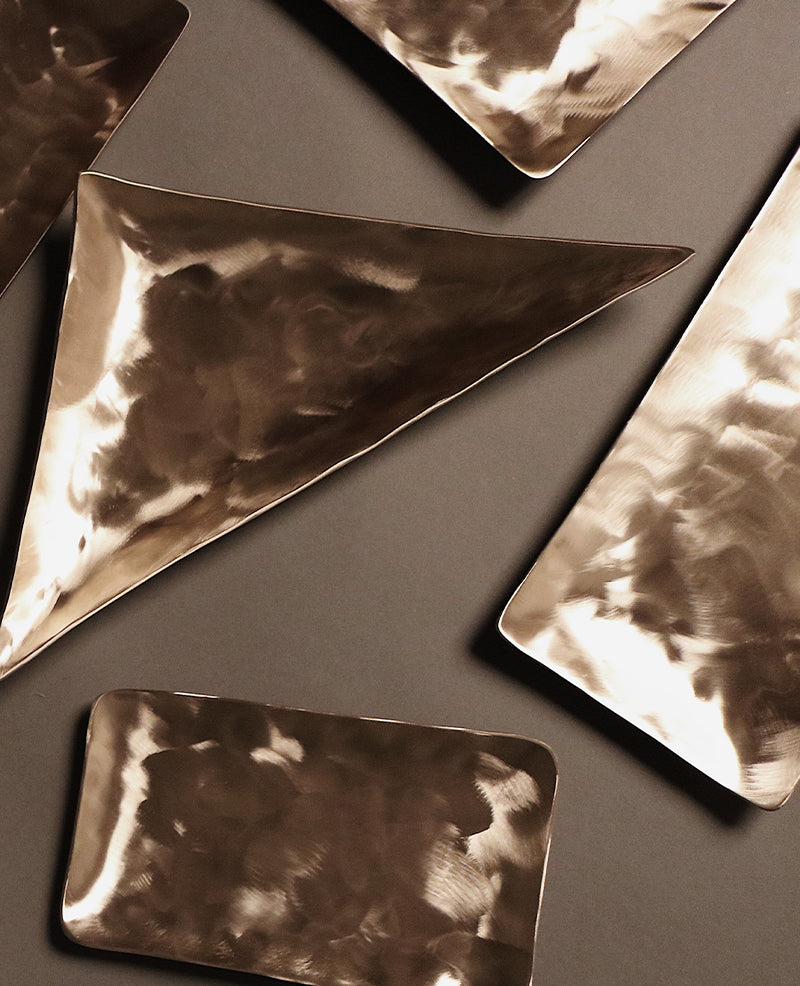
1. Hand-forged plates in different forms
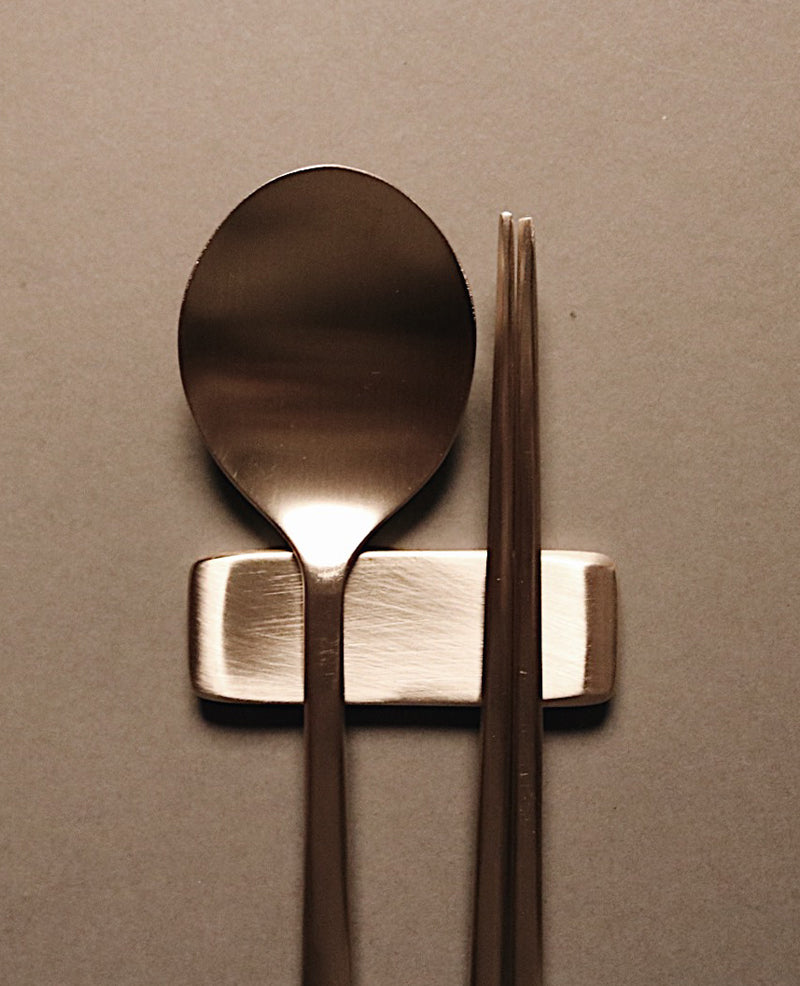
2. Traditional Korean spoon and chopstick sets
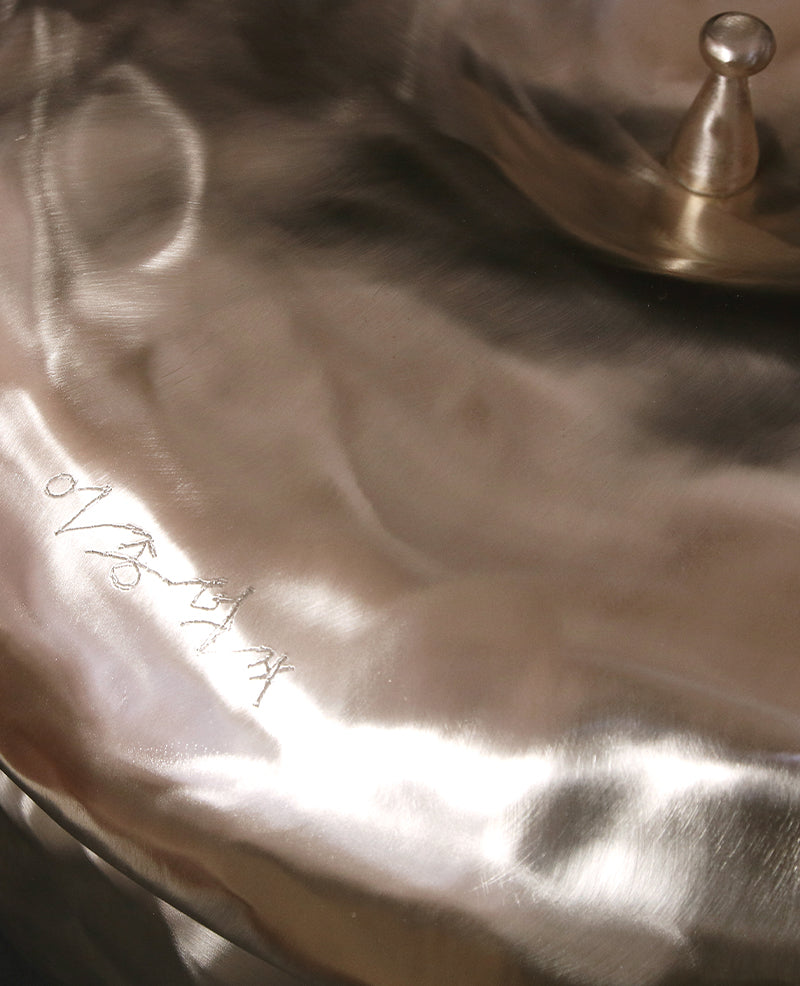
3. Detail of 항아리
(hangari)—a small jar with Jong Duk
Lee's signature
- 방짜 (Bangjja), homegrown bronzecraft.
For multiple decades Korea’s Jong Duk Lee has been
pursuing perfection in the ancient craft of bangjja, which is a unique form of
metal work. Bangjja comes from the Napcheoung region in the country’s north,
where it was originally used to make bell instruments and also tableware and crockery. Lee has dedicated much
of his life to applying the bangjja technique to traditional instrument and
object making, earning an intangible heritage qualification in Korea. He also encourages others to pick up the
remarkable craft through education of younger
artisans, but today 80% of all the bangjja instruments (such as jing and kkwaenggwari) made in Korea are by Lee.
Based in Tokyo, Ryutaro Yoshida has similarly pursued a
career dedicated to craft in Japan as the co-founder of Time & Style - a respected design and furniture brand. It
produces pieces for famous architects such as Kengo Kuma and sells its designs through various retailers
across the world. For Yoshida, Time & Style is
defined by its close relationship to the craft culture of Japan and he enjoys working alongside artisans
across the nation to form products that honour the past but are also appealing to a contemporary audience.
With this in mind, Yoshida was interested in speaking
with Lee about bangjja, a craft he’s curious to learn more about. It’s
also a craft form that could
die out – something that Yoshida’s work in Japan aims to prevent for its craftspeople. Younger generations
have not been able to move bangjja forward and the Korean government is
not giving the craft
enough support. But there is immense importance in bangjja - with its
incredible history and the meticulous making process behind it, it forms some of Korea’s most beautifully
made products, as Yoshida
and Lee discuss.
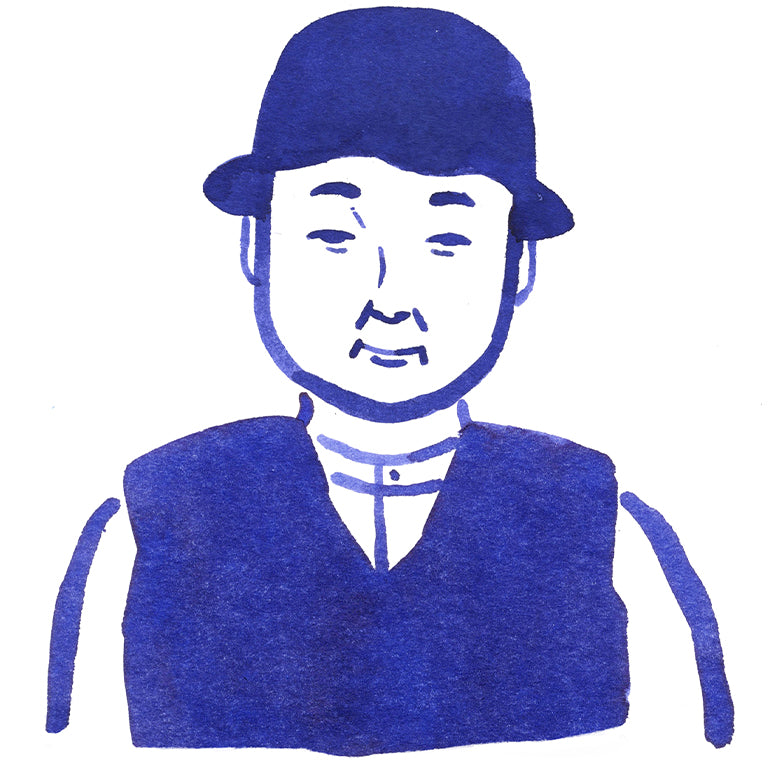
Jong Duk Lee
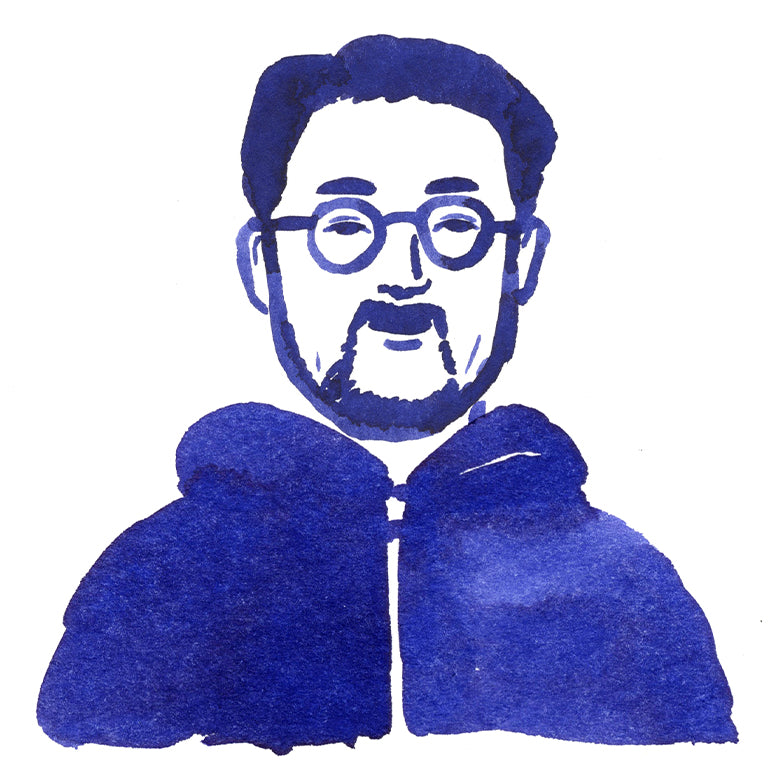
Ryutaro Yoshida
Illustrations by
Jiye Kim
- I am working with more than 200 artisans all over Japan with various kinds of craft for around 25
years so I’m familiar with the long history and tradition. However, bangjja is a type of craft that
only exists in Korea and I don’t know much about. I am very interested in its history - how long has it
existed? Do you know from where it originated?
- Bangjja craft goes back to Goryeo period (beginning in 918AD), so
it has existed for about 1000 years. However, bangjja was not a
common craft even all those years
ago. I’m aware that some Japanese crafts came from Korea, but the iron casting craft that you are
familiar with in Japan was also widely practised in Korea and it is a different technique to bangjja, which was historically used to make tableware for the royal
family or to make traditional Korean metal instruments such as jing
and kkwaenggwari. There have never been many craftsmen practicing
bangjja, but it has survived because it is so important to Korean
culture. I believe the technique behind it
originally came from India through Silk Road trading, but the specific blend of 78% copper and 22%
zinc that forms bangjja has only ever existed in Korea.
Yes, I saw the process of how bangjja is made, and it’s so interesting,
but also very labour-intensive. How did you get started and what made you want to start practicing bangjja? Was this craftsmanship a type of family tradition for you?
- About 40 years ago I used to work for a company that was manufacturing valves and plumbing screws,
so I was familiar with jumul (the more popular iron casting craft) and bangjja too. But I was
particularly interested in bangjja. I once watched Samul nori (a traditional Korean music form, played with jing and kkwaenggwari as instruments) and
I heard the sound and fell in love with it, so I decided I wanted to make the best jing and kkwaenggwari
with bangjja in Korea. I started working for a company that was making
bangjja, but they were cutting corners to save money and from there
wherever I went to learn
about bangjja I realised those practising it were not following the
traditional way. So I did more research and went to meet people who were on television for being
famous for their bangjja craftsmanship and I visited Japan and China
because I heard there were masters of the craft there - but no one was doing it the right way. So, I
continued to study by myself, looking at jing and kkwaenggwari instruments that have existed from centuries ago, researching
them and reading many historical documents. I would practice the techniques behind them
over and over in the workshop at the company when everyone else had left for the day. So, by picking
out the right technique from all the different sources – after lots of trials and error - I was
eventually able to master bangjja craft myself.
I am very surprised that nobody is practicing bangjja craft the right
way, because to me it seems like it is a symbolic craft in Korea. From my experience with Japanese
artisans, usually the craft is
handed down in families over many generations, so I find it amazing that you’ve become a master bangjja craftsmanship by researching, reading, and even visiting Japan and
China, all on your own. This is
similar to myself as I don’t come from a family of traditional artisans, but I am now working with
traditional craftsmanship.
- It’s nothing amazing really, making no money, I’m just doing what I love!
"I researched more and went to meet people
who were on television for being famous for their bangjja
craftsmanship and I visited Japan
and China because I heard there were masters of the craft there - but no one was doing it the right way.
So, I continued to study by myself, looking at jing and kkwaenggwari instruments that have existed from centuries ago,
researching them and reading many historical documents."
No, I think it’s great. I am working with many artisans to design new products that can be used today by
using traditional craftsmanship. In this way we can continue to use the craft for the next generation. Is
this something you are
interested in doing?
- Yes of course. I’m trying to make something new every day. You get a little tired of making the same
instruments, and tableware after a while! I tried to make many different items with bangjja
craft, such as candle holders and plates, wine coolers and dishes that are not just round. I tried
also making rings and bracelets and such, but all the jumul factories
would copy me, so I stopped
making them.
Ah, but that’s great to hear that you are always trying new things, but also sad to hear you cannot make
money. With the bangjja process, it is so labour-intensive but all of this
effort is what make
the final products so beautiful. The process is not close to iron casting at all, but it reminds me of the
way to make katana (a Japanese sword) where a craftsman is constantly
heating and hammering the
product, but they are working with a ready-made plate. Can you explain the bangjja process a little bit? And what’s your favourite part of the process?
- That’s right, with bangjja nothing is ready-made. You first have to
get the raw materials (copper and zinc) and melt them together in the right proportion to get to 1200
degrees Celsius. Then you
pour it out onto plate frames, and mould it together and then start pounding the plates while they are
hot. I think this is the most important part but also the most difficult. To know when to take the
plate out from the fire before
it melts away completely, and once taken out, knowing how many times you can pound it before it breaks
is very tricky. This is something you can only learn by experience, by feeling the right temperature
on your body for example.
After more heating and pounding, you dip the piece in room temperature water, where the form you have
worked so hard to create loses its shape, but this will make bangjja impossible to break. Then you
must hammer it one last time to
get the final perfect shape and polish it with a hand grinder. My favourite part is seeing the end
result, creating a form that I imagined in my head after going through this entire process.
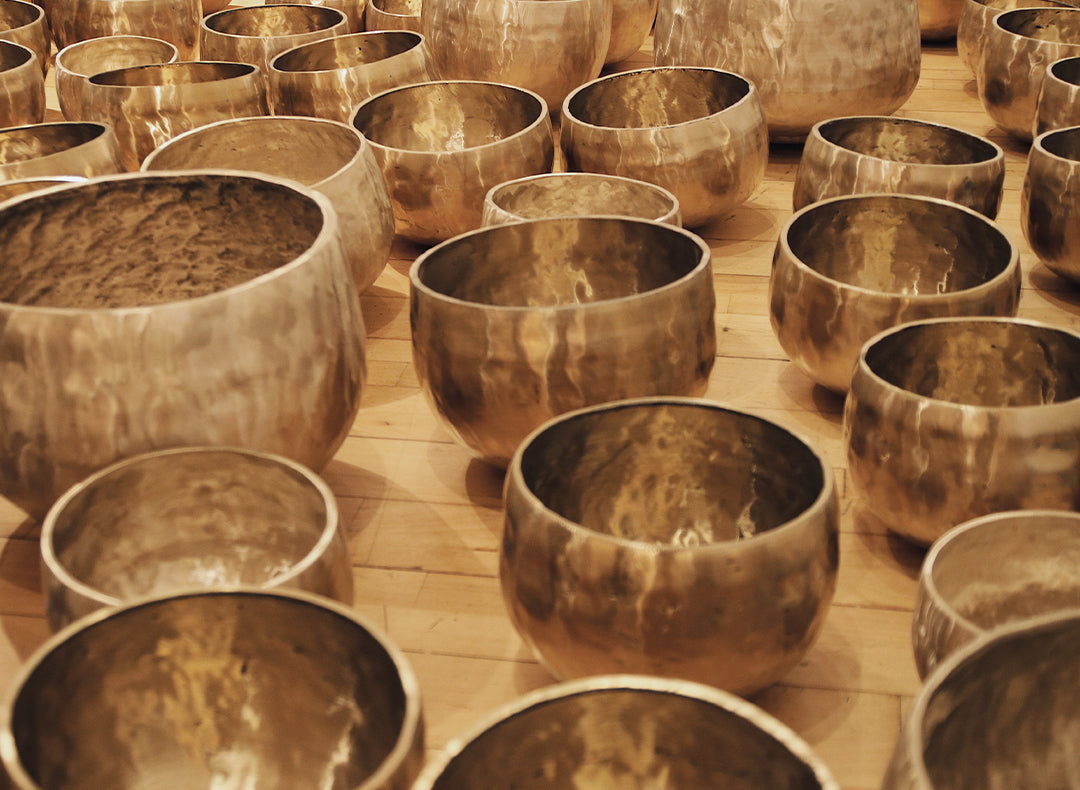
4. 종
(jong)—singing bells for a traditional Korean musical event
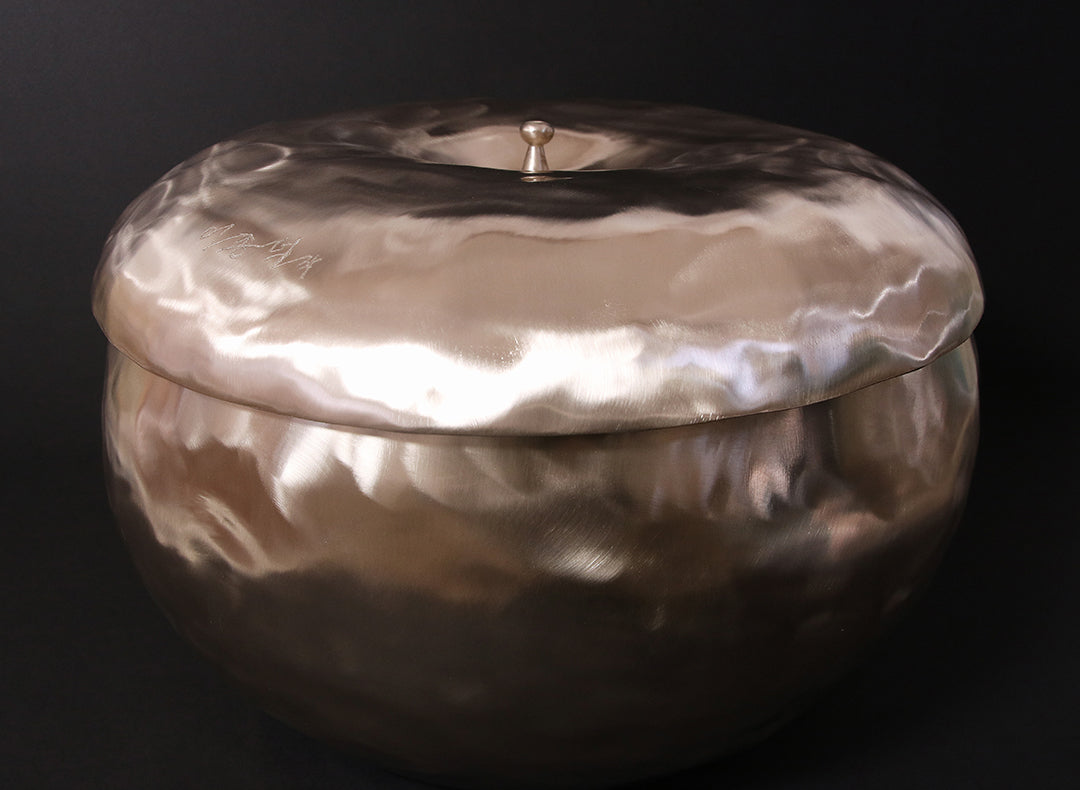
5. 항아리
(hangari)—a small jar
- Because it is such a labour-intensive process, done in such a harsh environment, do you have any young
people coming to learn the craft?
- I’m sure no one wants to be in such harsh environment, in such heat! In my studio, I find that
people who came here to learn often give up and leave. But, now I have one young man who’s been with
me for about two years, he can now
make two kkwaenggwari and two jing by
himself in a day, which is very impressive. I would say there are less than 10 people who have
mastered the technique from me and
are now active on their own. And that’s not enough people - I have a feeling it’s a craft that will be
lost and forgotten in the future.
"My attitude was that this craft should
only be practiced by Koreans, because it’s from here. But I was foolish to think like that, craftsmanship
belongs to everyone no
matter where they are from, it belongs to anyone who wants to learn it and continue it."
Yes, this is also a similar situation in Japan as well, a lot of crafts are disappearing, because the
lifestyle has changed to a Western lifestyle and we have also lost many Japanese traditions. However, many
craftsman are supported by
the government and any craft that have existed for more than 100 years receive funds from the government.
Also, in the last 10 or 20 years, more young people are getting involved, like me. And they try to translate
traditional crafts to
products that are more suitable to today’s market. What’s your feeling if younger designers come and
approach you for collaboration? Because from my experience, some artisans don’t want to collaborate because
they have their own vision,
and own way of working.
- Unlike Japan, we do not get much funding from the government dedicated to preserving traditional
crafts. Because I hold this intangible cultural heritage certificate for the region I do get a small
grant from the government to teach
bangjja. However, I am the one of the very few teachers for this craft
and sadly I cannot teach everyone who comes to me to learn and support all the facilities by myself
financially. I am always open
to working and collaborating with others. Years ago when I was much younger, foreigners used to come to
me to learn bangjja craftsmanship, my attitude was that this craft
should only be practiced by
Koreans, because it’s from here. But I was foolish to think like that, because craftsmanship belongs to
everyone no matter where they are from, it belongs to anyone who wants to learn it and continue it. I
really hope there will be
lots of young people who are creating even more beautiful products with bangjja craftsmanship in the
future and trying to make new designs with it.
I’m so impressed about how you talk about Korean craft, how it doesn’t belong to just Korea, but to
everyone in the world, it’s a nice way to think as a craftsman. We are currently living through a difficult
time, but I think once it's
passed, people will look for products that are more longstanding, and appreciate the value of craft even
more. I know a lot of metal workers, but I don’t know anyone who works the way you work. I think it’s so
special, and impressive. In
future I would love to work together. Thank you so much for sharing not only your work, but also your life
story.
INTERNATIONAL VOICE
RYUTARO YOSHIDA
Alongside his brother Yasushi, Yoshida founded Time &
Style three decades ago and today it operates from its main office in Tokyo and its furniture production
facility in Hokkaido. In
Hokkaido the company works with some of the world’s best timber from slow-growth forests to craft fine
furniture, coveted by the world’s best architects. Yoshida also adds to the full Time & Style product range
alongside some 200 Japanese
craft artisans who occupy work-shops across the country. In collaboration with this craft talent Yoshida
actively seeks out (often from driving from one small village to another to discover them) Time & Style have
added many magnificent
items to its catalogues from hinoki wood trays to bronze legged dining tables.
JONG DUK LEE
www.bangjjayougi.com
RYUTARO YOSHIDA
www.timeandstyle.nl
INTERNATIONAL VOICE
RYUTARO YOSHIDA
Alongside his brother Yasushi, Yoshida founded Time &
Style three decades ago and today it operates from its main office in Tokyo and its furniture production facility in
Hokkaido. In
Hokkaido the company works with some of the world’s best timber from slow-growth forests to craft fine furniture,
coveted by the world’s best architects. Yoshida also adds to the full Time & Style product range alongside some 200
Japanese craft
artisans who occupy work-shops across the country. In collaboration with this craft talent Yoshida actively seeks
out (often from driving from one small village to another to discover them) Time & Style have added many magnificent
items to its
catalogues from hinoki wood trays to bronze legged dining tables.
JONG DUK LEE
www.bangjjayougi.com
RYUTARO
YOSHIDA
www.timeandstyle.nl
Bangjja is a Korean form of hand-forged
brassware, which tends to be created in the Napcheong northern region in the country’s north. The material for
bangjja is a specific blend of 78% copper and 22% zinc, which is melted
together
and then hammered into shape while still hot and malleable. The more the metal is pounded the more robust it
becomes making for a
highly durable material perfect for use in tableware.
Because of its unique composition, bangjja is known to be self-sterilising and
the way it conducts heat means it can keep hot food hot and cold food cold for long periods. Bangjja however, is not only used in tableware, it is also applied in the creation
of a Korean traditional instrument called jong (a type of a gong). The jong, hand-forged by bangjja
artisans, can be customised to make different tones through different shapes and thicknesses of the
instrument’s
design. This hand-made process is seen as a work of art and a traditional custom in Korea that continues to be
coveted.
Bangjja brassware is produced using techniques that have been handed down over
thousands of years. These products are so hardy that even pieces made centuries ago are rarely bent or broken.
Today, Korean people
are increasingly recognising the benefits of brass tableware, but most products on the market tend to be
machine-made using a process called jumul. While bangjja brassware
requires a more labour intensive and expensive process to make, it is a better product that is longer-lasting.
The rare craft behind it should not be forgotten.
1. Copper and zinc are melted together at a temperature of 1200 degrees.
2. The melted substance is poured into plate frames.
3.
Nepimjil – is the process where a group of artisans gather together and
hammer the hot plates in unison to make them thinner.
4. The process of layering the thin hammered plates and shaping them into a bowl is
woogimjil.
1. Copper and zinc are melted together at a temperature of 1200 degrees.
2. The melted substance is poured into plate frames.
3.
Nepimjil – is the process where a group of artisans gather together and
hammer the hot plates in unison to make them thinner.
4. The process of layering the thin hammered plates and shaping them into a bowl is
woogimjil.
5.
Dakchimjil is the next step that once again requires artisans to gather
together and hammer and stretch the metal into shape.
6. The still-hot metal is then dipped in cold water, increasing the hardness of
bangjja without making it brittle.
7. After being dipped in water the form is lost and
byerumjil is the process
of re-hammering the metal into its final form.
8. A machine is used to remove uneven imperfections and smoothen and polish the surface of
bangjja. This process is called
gajil.
5.
Dakchimjil is the next step that once again requires artisans to gather
together and hammer and stretch the metal into shape.
6. The still-hot metal is then dipped in cold water, increasing the hardness of
bangjja without making it brittle.
7. After being dipped in water the form is lost and
byerumjil is the process
of re-hammering the metal into its final form.
8. A machine is used to remove uneven imperfections and smoothen and polish the surface of
bangjja. This process is called
gajil.
9. Finished product -
jong, a traditional Korean bell instrument.
10.
Soban – a table for one made from the versatile material that is
bangjja.
9. Finished product -
jong, a traditional Korean bell instrument.
10.
Soban – a table for one made from the versatile material that is
bangjja.
© Images provided by
– Korea Cultural Heritage Foundation
– Cultural Heritage
Administration